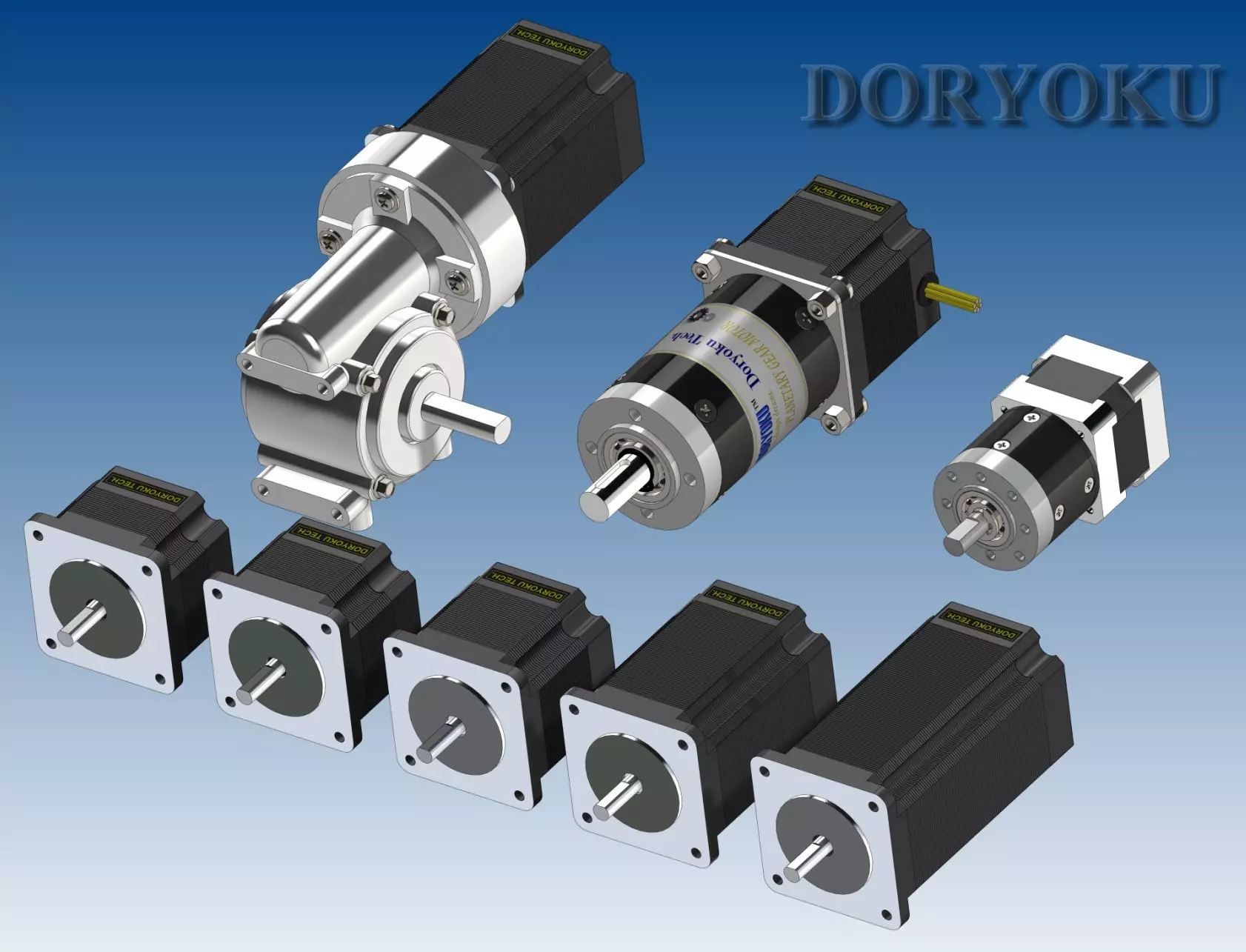
Stepping Gear Motor
Stepper motors or stepping motors working principles is using the magnetic properties between numerous stator and rotor teeth. The pulse signal can determine how fast the dipole of the magnets change so we can further control the rotation of the stepper motor.
Stepping motor has a rated voltage and current. A typical case like stepping motor NEMA 23 (stepping 56 type) might have a rated voltage of 2.9 Volts and a maximum current of 2.0 Amps. It means if you hook it up to 2.9 Volts it will draw 2.0 Amps.
If you run it at a higher voltage it will consumptive more current and get overheat. That's why we don't suggest customer hook motors straight to a voltage source. we don’t suggest you use a stepping motor driver. Stepping motor drivers control and regulate the current. If you hook it up to 10V, even the motor try to offer more current, but the stepping motor driver will change away from using frequency pulses to limit the average current.
ADVANTAGES
◎ Rotation speed: A stepper motor can rotate proportionally to the input signal, as a result, it can be operated without any feedback mechanism. With a higher frequency of incoming pulse, the rotation of the motor would be continuous and its operating speed also increases. Since the frequency of the input signal can change the angular speed, out stepper motor can be decently customized to a very wide range of commercial applications.
◎ Vibration less: Unlike the other motors activated by the friction between teeth, the magnetic interactions of hundreds of stators and rotors allow the motor to rotate in 1.8° in every step. Frictionless operation means no vibration during the rotation, which is an important property of industries like semiconductors or advanced electronic devices.
◎ Accurate positioning: The average error of positioning of a stepper motor is 4%, and attribute to the characteristic of the magnetic mechanism, the positioning error will be regulated in every step. Through the feedback of position sensor, you could control the torque and speed with ease. The precision of the operation is especially significant to the repeatable working steps process.
That's why stepping motors are used in various types of equipment for lots of applications like 3d Printer, Laser device Printer, CNC Router, Engraving, Industrial Application, Food Machine, Automatic, Production Line, Milling, Lathe, etc.
You could also combine stepping motor with Planetary or Worm gearbox.
Stepper 42, 56, 86 and Nema 17, 23 option.
Features
- Bipolar 4 wires
- Unipolar 6 wires
- Worm Geared Stepper Motor Ratio 1/10, 1/15, 1/30 with Output shaft 10mm
- Nema 23 stepping motor with Worm gearbox, Planetary Gearbox.
- Planetary gearbox option.
- Applied to 3d Printer, CNC Router, Engraving, Industrial Application, Food Machine, Automatic, Production Line, Milling, Lathe , etc.
Customized design welcome
- DORYOKU can provide special shaft or flange version upon request. Gearbox design, Shaft Material, Flange shape and IP level can be made according to your requirement.
Stepper Motor ST56XS
ST56 XS
Nema 23 39mm length stepper motor. Planetary Gearheads / Worm Gearheads Available.
DetailsDC Stepper Motor ST56S
ST56 S
Nema 23 44mm length stepper motor. Planetary Gearheads / Worm Gearheads Available.
DetailsDC Stepper Motor ST56M
ST56 M
Nema 23 52mm length stepper motor. Planetary Gearheads / Worm Gearheads Available.
DetailsDC Stepper Motor ST56L
ST56 L
Nema 23 78mm length stepper motor. Planetary Gearheads / Worm Gearheads Available.
DetailsDC Stepper Motor ST56XL
ST56 XL
Nema 23 103mm length stepper motor. Planetary Gearheads / Worm Gearheads Available.
DetailsStepping Gear Motor - | High Torque Worm Gear Motors Manufacturer Since 2000 | Doryoku Technical Corp.
Based in Taiwan since 2000, Doryoku Technical Corp. is a DC gear motor manufacturer. Their main products, including Stepping Gear Motor, DC Planetary Gear Motors, Worm Gear Motors, Spur Gear Motors, which can be brushed, BLDC, stepping, NEMA, brushless, or with servo motors combined.
DORYOKU is one of the leading DC servo motor | DC gear motor manufacturers since 2000 based in Taiwan, and is specialized in producing high torque dc motor to meet the needs of automation applications. Our DC gear motor such as, planetary gear motor, DC servo motor, brushless DC motor are designed with size range from 18mm to 80mm, gear ratios ranging from 4:1 to 11909:1. and continuous torque of up to 4,166 oz-in! We offer a cost-effective solution for your automation requirements. The product line includes planetary, Worm, spur Gearbox, combined with brushed, BLDC, stepping, servo motor.
Doryoku Tech. has been offering customers high torque DC motors and DC gear motors, both with advanced technology and 25 years of experience, Doryoku Tech. ensures each customer's demands are met.